Product Timeline
Lamps that lived before. Check how our lights have developed through the years. From the very first sprung desk lamp to the latest precision engineered Type 80 range. Our portfolio of collections have evolved to include floor lamps, multiple wall light designs and ceiling lights. Designed by George Carwardine, Sir Kenneth Grange, Anglepoise Design and with various Editions by Margaret Howell, Paul Smith and collaborations with The National Trust.
They range in size from Mini to Giant, which is your all time favourite? Do you own a piece of Anglepoise History?
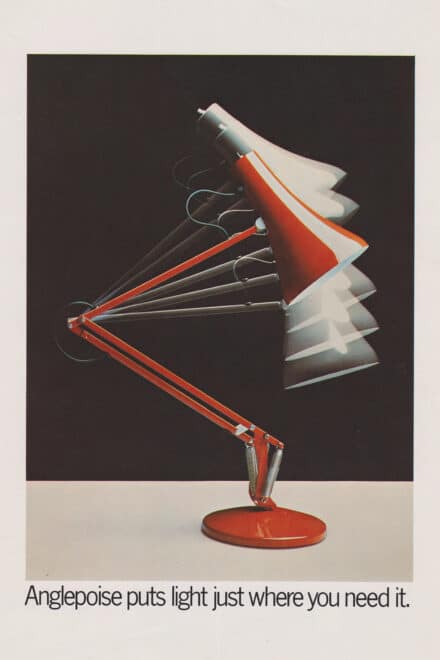

Product History Timeline
Take a trip down memory lane
2019
Type 80™
Designed by renowned British industrial product designer Sir Kenneth Grange in his 90th year, the Type 80 is an all-new design that’s distinguished by a striking, graphic profile. Every detail has been carefully considered and precision engineered to deliver streamlined style, ease of use and consistency across the collection.
2018
90 Mini Mini
The 90 Mini Mini has all the versatility and personality of a classic Anglepoise lamp wrapped up in its tiny form. The 90 Mini Mini is powered by USB for enhanced portability and has a dimmable integrated LED. At half the size of a standard lamp it’s designed to fit just about anywhere.
2017
Original 1227™ Mini Ceramic
Formed from the purest bone china, the white, gloss-finished shades or our Original 1227™ Mini Ceramic lights turn translucent when turned on, radiating a soft, ambient light around the room.
2015
Original 1227™ Mini
Scaled down to two-thirds of its original size, the Original 1227™ Mini Collection is playful, more versatile and contemporary version of our most iconic and best loved 1930’s Anglepoise® design.
2011
Type 75™ Mini
Designed by Sir Kenneth Grange as a scaled down, more playful version of the best selling Type 75™ design.
2011
Type C™
Created by Sir Kenneth Grange, this remarkable lamp incorporates touch sensitive dimming, light level memory, energy efficient LED’s and a balance mechanism that responds to the lightest touch. The result is a seductive form that adds a level of sophistication and elegance.
2008
Type 1228™
Designed by Sir Kenneth Grange in 2008, Type 1228™ offers all the functionality of the traditional Anglepoise®, but with a more contemporary aesthetic and exceptional versatility.
2004
Type 75™
Designed by Sir Kenneth Grange, Type 75™ is inspired by a 1970’s version of the Anglepoise® Apex 90®, originally launched in the 1950’s. Grange reinterprets the modernist lines and no-frills functionality of its predecessor for new generations.
2003
Type 3™
Sir Kenneth Grange’s first lamp as Anglepoise® Design Director, the Type 3™ featured chrome plated solid steel and was influenced by the earlier Original 1227™ lamps by George Carwardine.
1985
Apex 90
The Apex 90 was designed to be a modern take on the Original 1227™.
1973
Model 90
The Model 90 introduced a range of colours, including one that inspired Margaret Howell’s Yellow Ochre colour to the Type 75™ lamp that’s available today.
1960
Model 75
The Model 75 became one of the inspirations behind Kenneth Grange’s Type 75. It is one of the earliest designs featuring a different shade shape from our Original 1227™.
1938
Model 1227
The Model 1227 added many smaller design details, such as the removal of the small shade vents on older iterations. It also saw the introduction of the two-step base, which is consistent with all our Original 1227™ lamps today.
1935
Model 1227
The Model 1227 was an evolution of the 1208, making it more suitable for a domestic environment. It is commonly recognised for its three-spring mechanism that’s available in our lamps today.
1933
Model 1208
George Carwardine licensed his design to spring maker, Herbert Terry & Sons, who already supplied the springs for his lamps. Not long after, the Anglepoise® name was registered and the 4-spring ‘Model 1208’ went into volume production.
1932
Model 1208 Prototype
In 1932, car designer George Carwardine unveil his remarkable invention – a 4-spring lamp, combining unprecedented freedom of movement and perfect balance due to its patented constant spring mechanism. Soon demand for the lamp far outstripped Carwardine’s small-scale supply, so he sought the help of Herbert Terry & Sons.
“Its almost person-like quirkiness, along with its technical perfection, makes the Anglepoise inherently British. The confluence of industry that led to this creation is my family’s heritage. I’m the 5th generation doing this, since my great-great-grandfather Herbert started it all in 1855. The Anglepoise name has been trading for 90 years. The secret to this kind of longevity? Well, actually caring is a start.”
Simon Terry – Custodian of Anglepoise
Date your Anglepoise
If you’re lucky enough to own a piece of Anglepoise history, whether it’s tucked away or displayed pride of place – have you ever wondered how old it is? We want to help you figure this out, check out how to date your Anglepoise.